By Dick Otte, CEO, Promex Industries
Medtech and biotech devices are uniquely suited to benefit from emerging electronic capabilities – specifically, the kind of electronics design, packaging and assembly offerings that are Promex’s specialty. With that said, these markets present a variety of manufacturing challenges and demands that require heterogeneous integration (HI) to address.
This two-part blog post provides a high-level overview of the current HI environment, including:
- Convergence of medtech and biotech with electronic and non-electronic content;
- How to pursue manufacturing and assembly of converged devices;
- HI project development and case studies; and
- Factors to consider when selecting a contract manufacturer.
Technology convergence
As the medical and biotech industries have evolved over the years, mankind has benefited from an ever-broadening range of capabilities, from new medicines and vaccines to advanced surgical techniques and DNA sequencing, to name a few. Information technology (IT) has continued to evolve in parallel with these advancements, making what was once the stuff of science fiction part of our everyday lives – with the integrated circuit and network connectivity helping to fast-track technology innovation.
Today’s environment represents a growing convergence of medicine and technology. New functionalities require a combination of electronic and non-electronic/mechanical content, such as high-power devices for automotive applications or adding flexible circuitry to traditional medical devices. This creating new manufacturing and assembly challenges that have given rise to HI assembly techniques.
What is HI assembly? Put simply, it’s a manufacturing approach that combines electronic and non-electronic content in devices to enable a range of complex functionality. Being well-versed in the convergence of medical and biotechnologies with microelectronics, Promex can engage with you to ensure that you know a) what you need for your project, and b) how to get there. This means determining what non-mechanical parts to use, developing a process to integrate all of the parts together, and building the devices in batches to ensure their functionality. Multiple steps are involved at each phase, as you can see in the heterogeneous assembly process illustration shown in Figure 1.
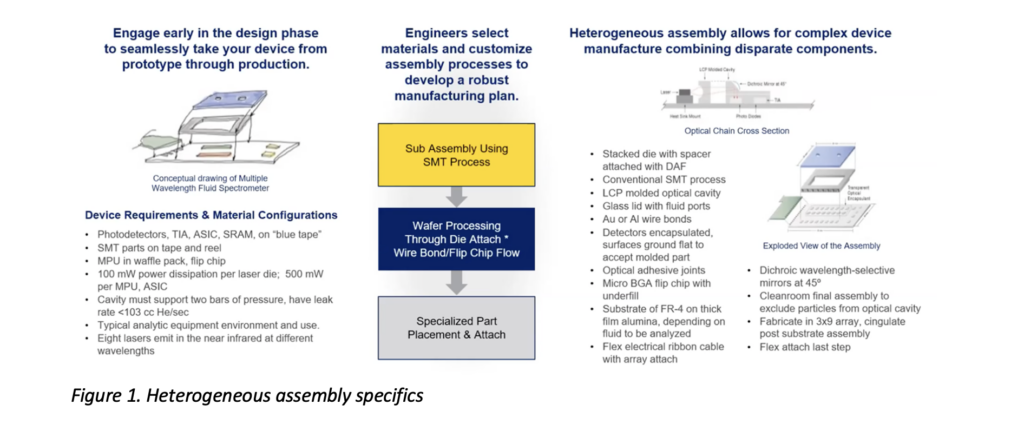
Manufacturing converged devices
Let’s take a look at some of the specifics of how devices transition from concept and prototyping to production. Traditional assembly follows a standard trajectory of process steps (Figure 2a) but isn’t designed to accommodate unique components and chemistries, and their associated challenges, that are integrated into the project design when dealing with converged HI devices.
For example, MEMS devices combined with a gyroscope are highly sensitive to touch and electrostatic discharge (ESD); power devices, which control multiple kilowatts of power, have issues with thermal conductivity and high voltages; and flexible circuitry that enables flexible devices has unique assembly requirements to accommodate its high tolerances.
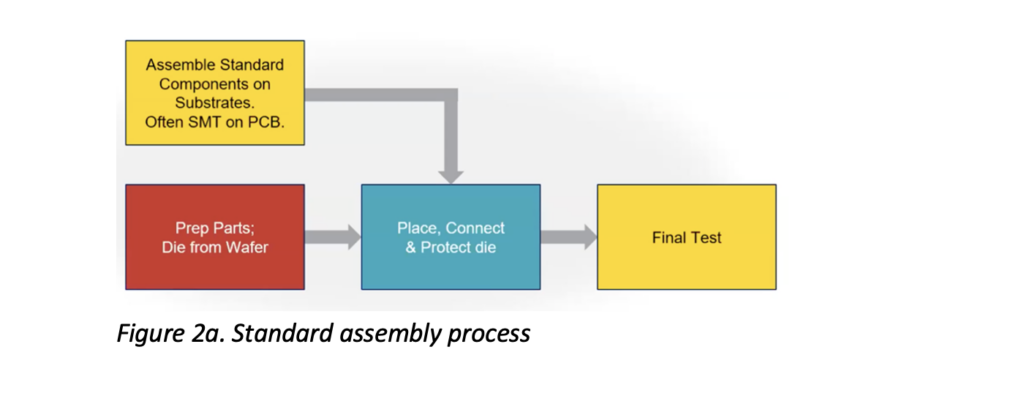
Figure 2b shows an adapted process that utilizes HI assembly techniques for converged devices. In this process, unique, non-electronic parts are added to the assembly at various stages based on their properties and preparation requirements – e.g., if holes must be taped to protect fluid content or if die-attach film (DAF) must be applied for ease of location.
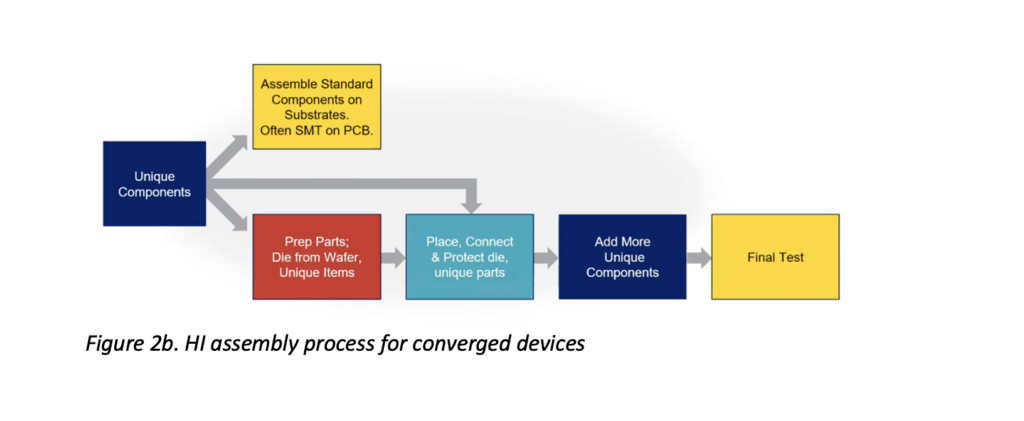
In the second part of this post, we will share some case studies of medical devices developed using HI assembly techniques, as well as tips for selecting the right contract manufacturer to meet your requirements.